The Responsible Blue Pants Collection
INNOVATIVE TECHNOLOGIES FOR A MORE SUSTAINABLE FUTURE
The Responsible Blue pants collection involves innovative and environmentally conscious technological processes that reduce the waste of water and the impact on the environment.
A more conscious approach to fashion, from raw materials to washing techniques.
DISCOVER MORE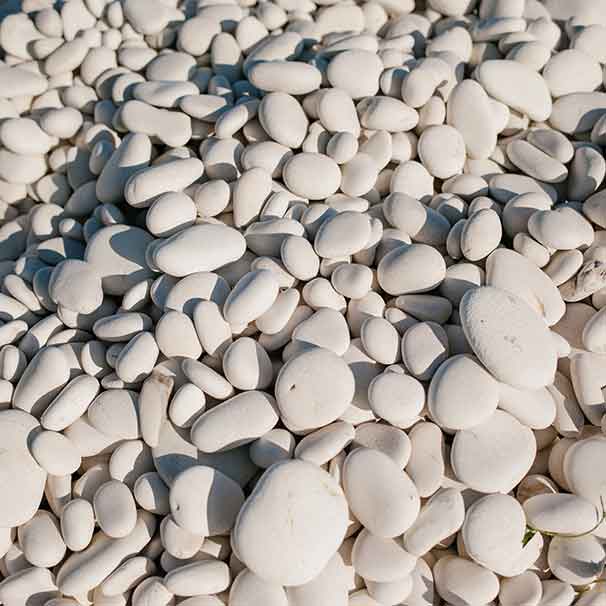
We select regenerated stone to create the typical lightening of jeans, this method significantly reduces the water consumption. The stone is insoluble, it does not absorb water and it releases far less dust than pumice: it is therefore easier and faster to remove. 20% of water saved compared to the traditional method that uses pumice stone.
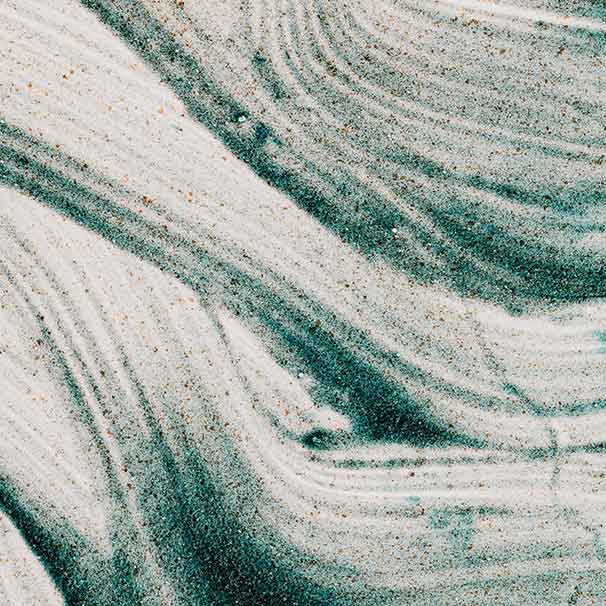
Mineral dyes are used both for dyeing and to give the dirty-denim-effect to the fabrics. By coloring with minerals, we reduce the energy consumption as the process takes place at much lower temperatures than a traditional dyeing procedure, also allowing an easier treatment of the wastewater.
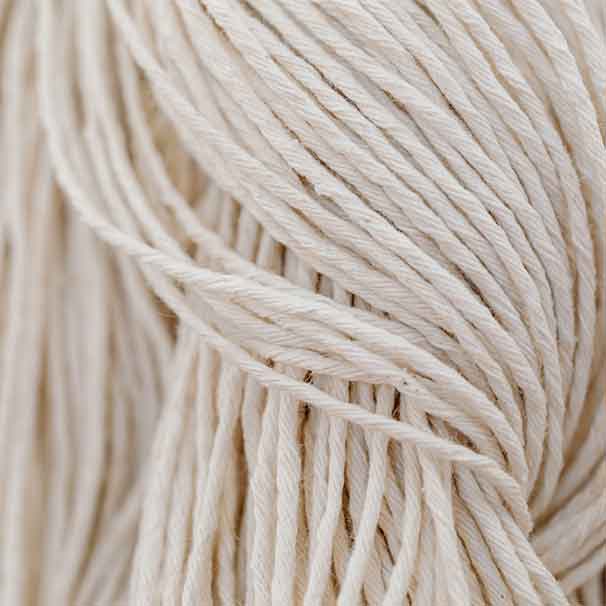
Lanolin is the natural solution chosen as fabric softener. It is a by-product originated from the first stages of the spinning process -the washing and cleaning phases– when wool still needs to be spun. The use of lanolin as a softener allows us to reintegrate a precious resource in the process cycle, avoiding its waste.